CAD Model Validation Excellence with CADIQ
ITI's cutting-edge product data validation solution, CADIQ, combines expert consulting in interoperability improvement with innovative technology to deliver industry-leading data validation services. Addressing design quality and product data interoperability challenges is crucial for enhancing downstream product data re-use.
Validation Solutions by ITI
ITI's product data validation solutions combine expertise in interoperability improvement consulting with innovative validation technology. Addressing challenges stemming from design quality and product data interoperability issues is critical to improving downstream product data re-use and successful MBD implementation.

Examples of Validation Scenarios:
Engineering Change Validation
- Identify quality and shape changes during engineering change requests.
- Verify the modified model's suitability for downstream use.
- Ensure all specified changes were made accurately.

Design Revision Documentation
- Identify quality and shape changes between design revisions.
- Verify resolution of previous quality defects.
- Check for unintentional changes introduced.

Legacy Design Data Migration Validation
- Compare CAD models and identify changes during migration.
- Identify quality and shape changes during legacy system migration.
- Evaluate different migration methods for optimal results.

Translation Validation
- Compare CAD models and identify changes during translation.
- Assess quality and shape changes introduced during CAD model translation.
- Compare translation methods for the best outcomes.
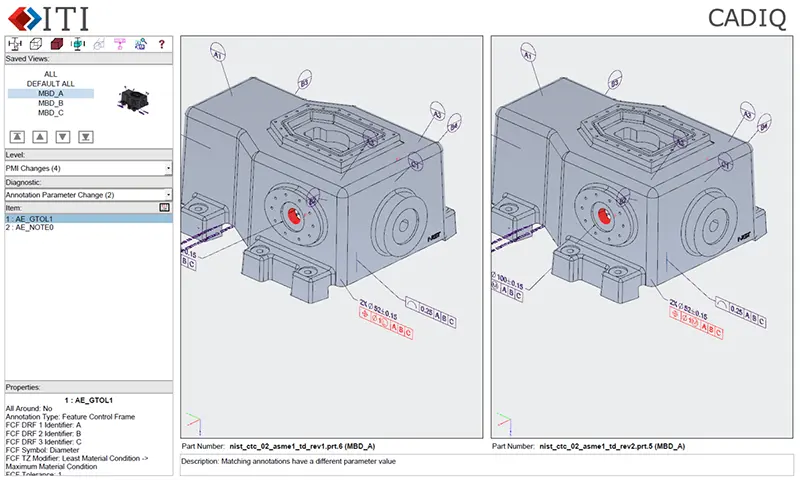
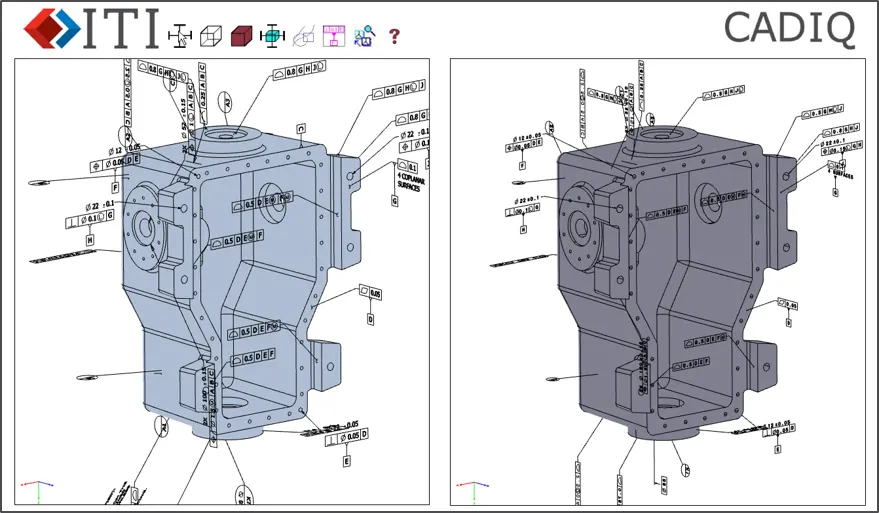
Native System Interfaces vs. Alternative Scenarios
While CADIQ advocates Native System Interfaces as the most robust validation approach, we understand that not all scenarios permit access to native CAD systems. This is particularly relevant for smaller suppliers adhering to OEM partner mandates or quality specifications. In such cases, procedures often mandate the validation of converted forms of original CAD master models to confirm the preservation of the original product design intent.
Elevate Your Design Quality and Interoperability
ITI and CADIQ have you covered with validation services across various operational applications. From ERP to CAD and database validation, our solutions ensure excellence in design quality and interoperability.
Contact us to explore how CADIQ can enhance your validation processes.